From the early manual mixing and coarse mixing, to the current mechanically integrated and fine mixing, powder mixing has undergone changes across the ages, and powder mixing equipment is constantly being upgraded,
such as the current double motion mixer, 3D mixer, etc. What kind of mixing equipment can solve some of the mixed problems that exist in 80% of the current enterprises? This requires a mixing equipment can solve such problems. These mixed problems are as follows. Only by fully understanding the problem we can find a suitable mixing machine to solve these problems and complete the
high uniformity mixing task.
1. Affect the material uniform mixing, the existence of centrifugal force in mixing motion, it can cause segregation of the mixed material with large difference in powder characteristics or large difference in density;
2. The mixture material can be agglomerated, clumped, and accumulated due to its own viscosity or particle properties, in this case,traditional three dimensional mixer can not effectively diffuse and mixing the material even if it is running, only the new
high efficiency double motion 3D mixer can overcome the above disadvantage. It is an ideal high performance mixing machine at present.
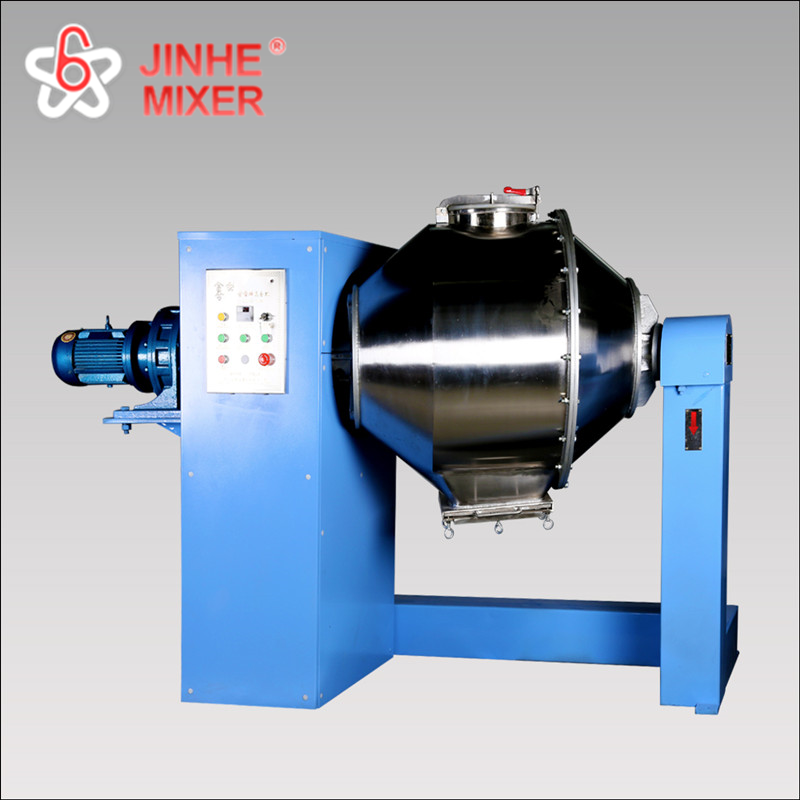
The
double motion 3D mixer has the advantages of quick discharge, no residue, medium-low speed operation and no segregation in the powder mixing application, at the same time, it has different series of mixer for high fineness, nano-scale materials or viscous lumps. Achieve uniform mixing of various powders.
The double motion 3D mixer of
Zhengzhou Jinhe Machinery Manufacture Co., Ltd. has a breakthrough in mixing efficiency, mixing uniformity and loading rate. Compared with traditional mixers, it has many mixing advantages and also has advantages in mixing time. Mixing the same batch of materials, the double motion mixer can reduce the time more than 50%, helping the company to save production costs. Moreover, the
loading rate can be as high as 85% or more, and one machine is equivalent to two machines.